The global automobile production has reached 100 million units per year, and continues to rise each day. With significant technology transitions, majorly being electrification, digital connectivity, autonomy and internet-based sharing; the raw materials needed for them has also changed drastically. In this recent ground breaking survey based research, it was found that modern automobiles are comprised of more than 2000 different chemical compounds made from 76 unique chemical elements of periodic table. So, out of 118 discovered elements; almost 65% of them are found in 1 single car. And, the detailed inventory discussed here later on, shows that electric vehicles are more vulnerable to material challenges than the gas guzzlers.
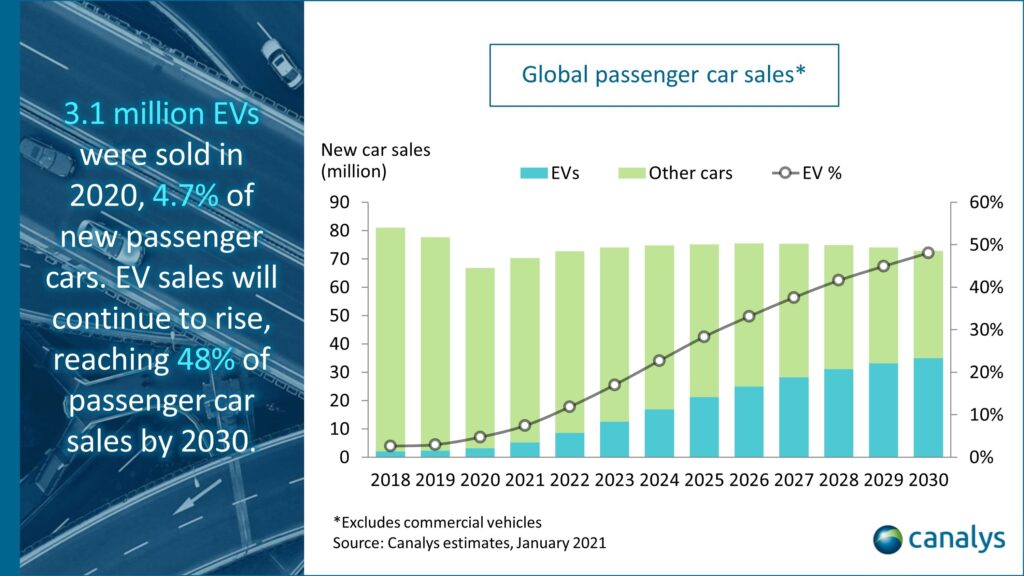
(source: businesswire)
Although the electrification is changing the future view of industry, it certainly has also changed the vehicle composition. And this change has potentially driven the supply risk vulnerability of materials used both in conventional and Hybrid Electric Vehicles (HEVs). This research is not just meant for literary reviews and debates to be held, but shows how the ‘unmindful’ and ‘inattentive’ trend towards electric vehicles is changing the recipe of automobiles and how this can disrupt the automakers.
The Research: Characterizing the Changes in Material Use due to Vehicle Electrification
Randolph E. Kirchain, a material research scientist led the MIT research group. The team gathered data sets from 7 sedans and SUVs manufactured in 2019-20.
2 PHEVs – Plug-in Hybrid Electric Vehicles
2 HEVs – Hybrid Electric Vehicles
3 ICEVs – Internal Combustion Engine Vehicles (normal automobile vehicles)
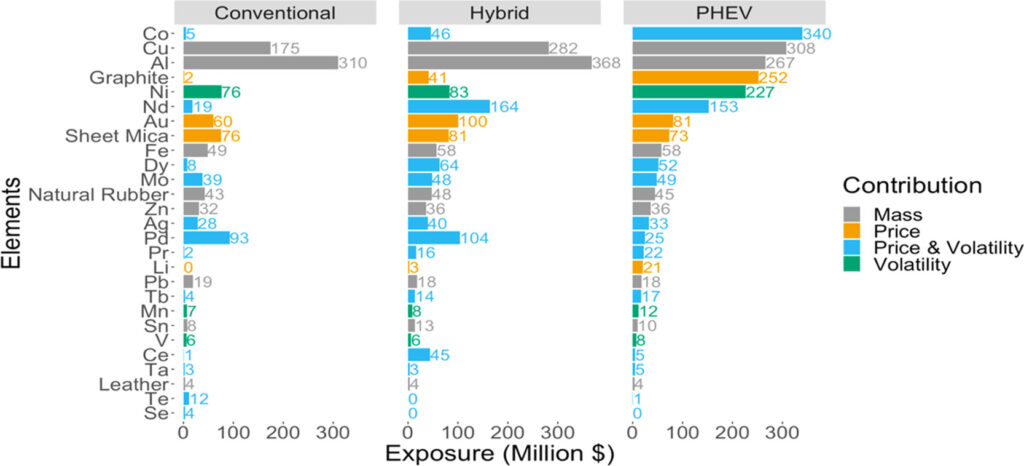
comprising of ICEVs, HEVs, and PHEVs
(Source: ACS Publications)
Team used data from International materials Data System (IMDS) such as part numbers, descriptions, weight of each material and much more to analyze material composition of each vehicle from 358,401 records. A “exposure” metric was defined, representing the cost to manufacturer from the material cost increase. Thus, elements present in the vehicle were also analysed on the basis of global production, trade restrictions, price volatility and other major factors. A machine learning AI algorithm was then developed to diagnose the supply risk of components and on the cost of final finished vehicle at the end.
The Electrified Exposure of Electric Vehicles: Which element Where?
The largest contributor to exposure in the engines and mounts subsystem is the turbocharger that uses Nickel (Ni) – based super alloys. Aluminum-castings and copper wiring dominate the transmission and clutch sub-system. Aluminum also drives exposure in the wheels, hubs and drums system.
One of the notable drivers of exposure are motors and electronics in Heat, Ventilation and Air-Conditioning systems (HVAC). And this is predominantly attributed by use of rare earth elements and sheet mica. Rare Earths also makeup the traction motors. Rare-earth elements like Nd, Dy, and Ce are present in large amount in hybrid and Plug-in Hybrid Electric Vehicles. The combined exposure from these materials is up to $268 million, a 10× increase from conventional internal combustion vehicles.
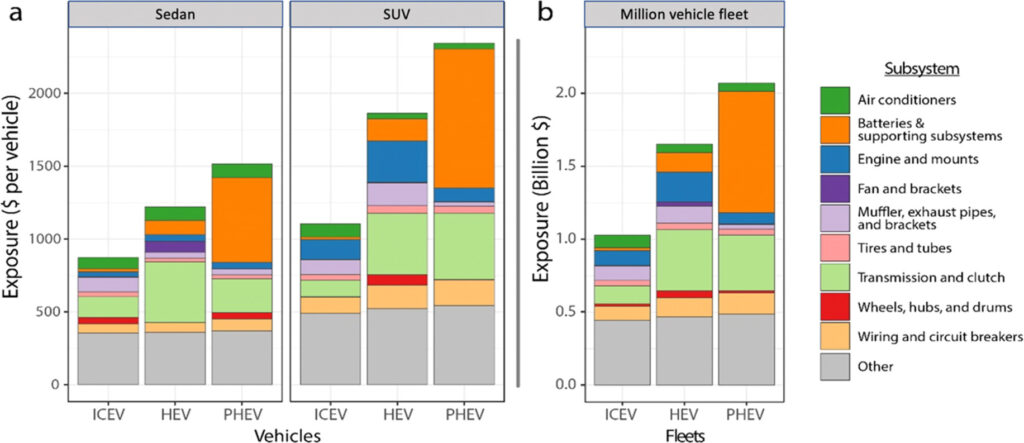
(Source: ACS Publications)
This was generic. For ICEVs. The above figure clearly shows that the recent advancements in the field of battery-related materials for PHEVs and HEVs; cobalt, nickel and graphite are the elements which are driving high vulnerability for automakers. However, in PHEV fleet Aluminum and copper represent 30% exposure and their prices even are much more volatile than steel and iron. Al per ton is 20x higher than Fe and that of copper is 50x higher. But still, Al and Cu are mostly used in body work and wiring.
Whereas, Cobalt, Graphite Carbon and nickel altogether account for nearly half of exposure for PHEV fleet. With this much electrification of automobile sector globally, their exposure has increased by around $716 million and growing. Of this, cobalt contributes $325M, graphite $254M and nickel $146M.
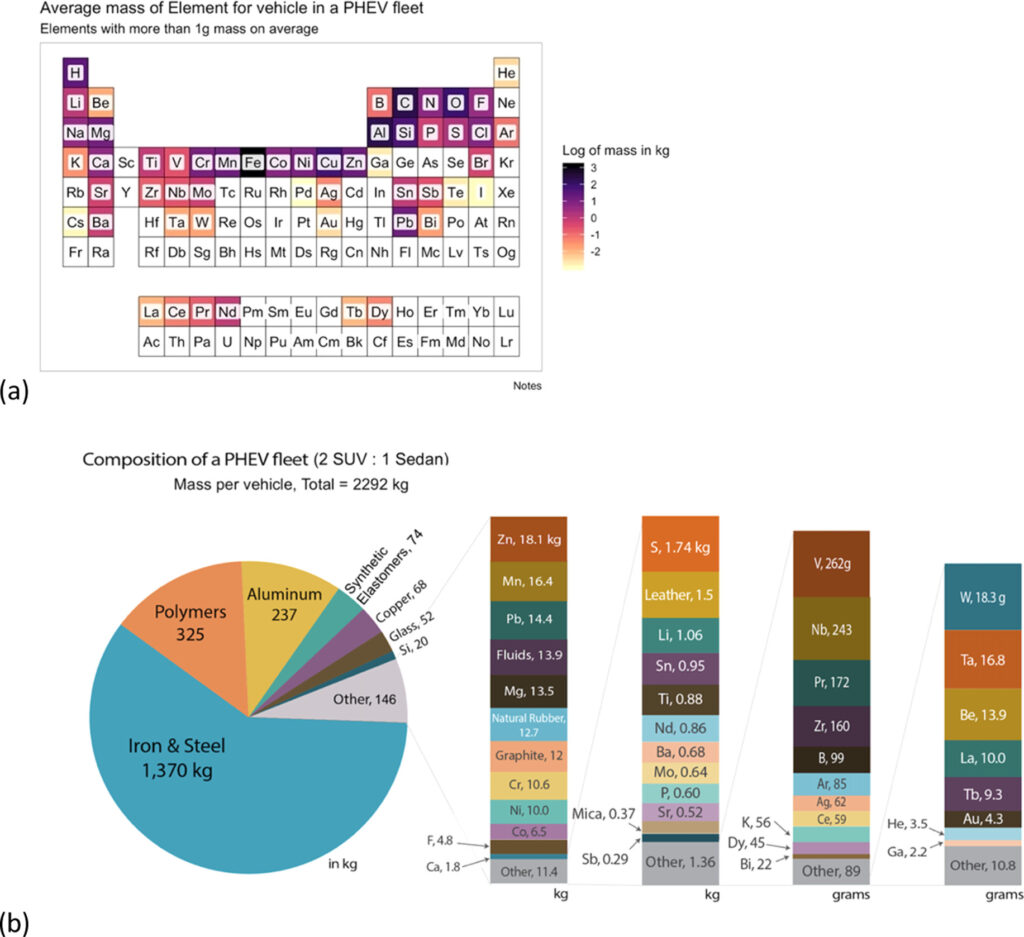
(Source: ACS Publications)
And the wonderful thing is that, arsenic is found in the lead-acid battery of the vehicle, krypton in the headlights and tantalum in capacitors. Another data to make your eyes wide open, is the use of gold, palladium and platinum. Yes, the use of these expensive, hard to get elements has increased by 10x in recent years due to their extensive use in sensors and chips, which will persist with increased level of automation.
The Supply-Chain Future: A feasible Transition to electric vehicles?
Is this the time to phase out the IC Engines? Electric Vehicles sector is booming and covering a large part of total automobiles production globally. But the electrification idea still remains far-fetched and many things are not taken in consideration. Government policies and subsidies for consumers, or a US-based giga-manufacturer ruling the sector is not enough.
Apart from developing infrastructure for electrification, the upshot is that for an automaker producing 1 million vehicles per year, a complete transition from internal combustion vehicles to plug-in hybrids would hike their total exposure from $1 billion to $2 billion. Kirchain imposes concern that, “policymakers and automakers should invest in research to reduce the use of critical materials, find substitutes, and build capacity to recycle more vehicle components at the end of their life.”
Manufacturers committed to produce only electric vehicles fleet by 2030 or 2040; must opt for this research phase too. Designing the prototype and phasing out humans with automation may seem fascinating, but this is what the reality is.