The World and its Economy suffered a major setback when ‘WHO’ as on 11 March 2020 declared Coronavirus as a Global Ongoing Pandemic. Many of us wanted to know the implications of this Pandemic on various industries. But the Logistics Industry was the only one that was plunged into a crisis that was yet to unfold. The Disruption in manufacturing and production, together with the shutdown, constrained supply chains, giving rise to critical shortages of Medical Equipment.
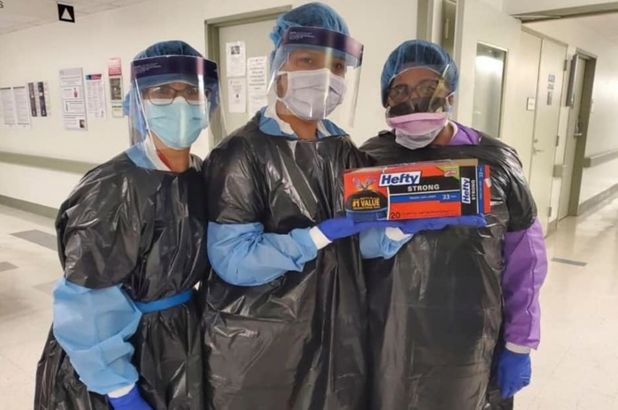
With the advent of government guidelines amid an ongoing crisis, there was a drastic increase in demand for medical essentials. An industry emerged to counter the Supply-Demand Misbalance along with Local help to achieve Extra-ordinary feats. Additive Manufacturing Industry termed as ‘Industry 4.0’ upgraded its capabilities to join the fight alongside the Healthcare sector against Novel Corona Virus.
Beginning of The Crisis
After the outbreak, there was a dire need for medical tests that are as much as reliable as rapid. Mainly two tests were approved for the detection of the virus; The Complete Blood test and the other is the Nasopharyngeal Swab test. The latter being rapid as well as simple to use, is deployed throughout the World.
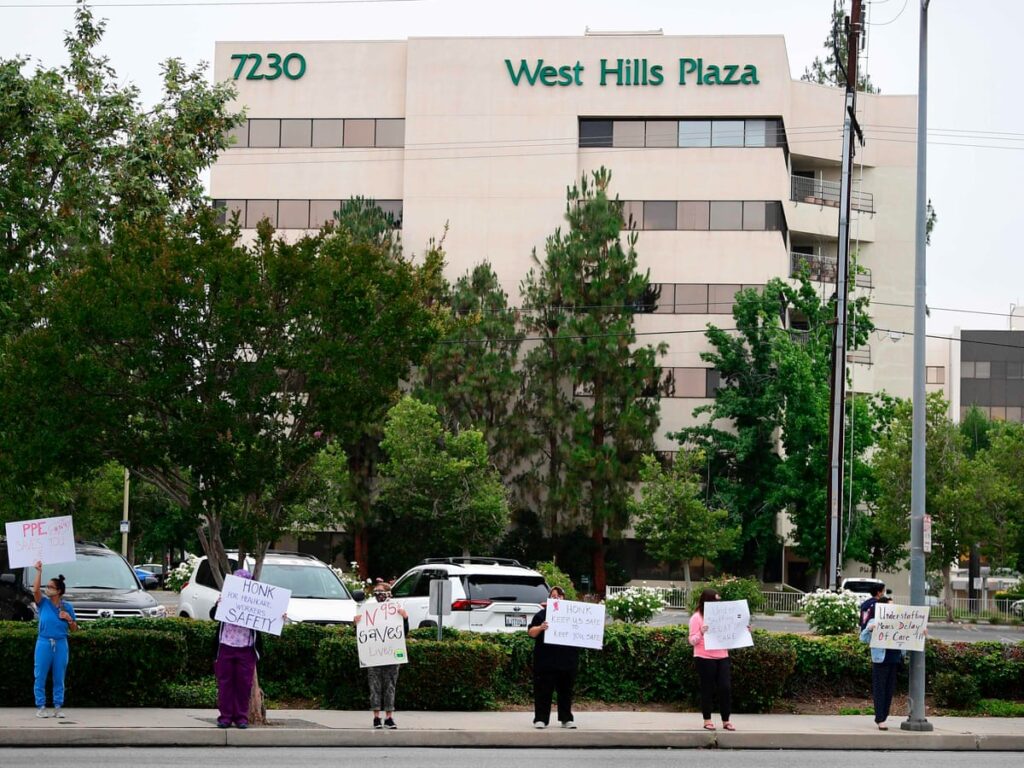
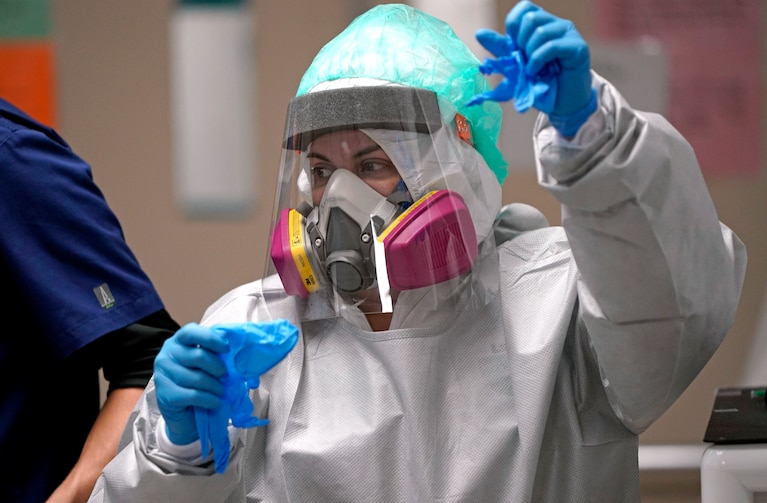
The Nasopharyngeal Swab is like a long pipe cleaner but with a very soft brush on the end. The personnel conducting the test would insert the swab from the base of your nose to touch the back of your throat. The soft bristles will collect a sample of secretion for analysis because the cells and fluids have to be collected from the entire passage for a good sample. Needless to say, the swab is a little bit uncomfortable, but it’s part of a procedure. I mean which medical test is ever comfortable!
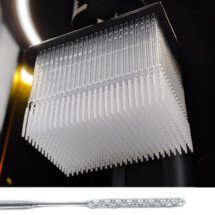
The problem began when the Nasopharyngeal swab’s demand sky-rocketed overnight. At that instant, there were not 10, nor 7 but only Two major companies that mass-produced them. One of those companies is Puritan Medical Products, based in Guilford, Maine. The overwhelming demand was tackled by ramping up the production to 1 Million swabs a week. Then the too U.S was facing a shortage, let alone the whole world.
Rising From The Ashes
The Lockdown was a big blow to all the existing Industries. After the disruption of airways, railways, and road transport systems, the production sector succumbed to high pressure and vast needs of Medical. The whole scenario was disturbing enough to see. An immediate response was needed from the locals due to the disruption of Logistics. That’s where these ADIs came into the field as a substitute but became much more. Highly encouraged people formed a network within days to save the lives of millions of people rekindling the Torch of Mankind.
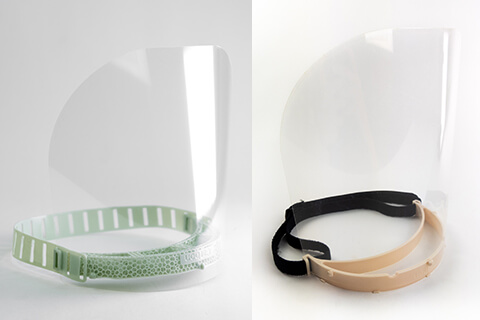
To cope with the challenge of providing the latest technology, and to save the lives of several people, ADI decided to create a highly de-centralized authentic network. Many companies, hobbyists, and enthusiasts formed an open-source platform of 3D printers to cater to their needs. Companies like Carbon™, FormLabs, and Issinova accepted the challenge and started to make various designs for a wide range of products. While many made certain progress in upgrading the technology like the TiO2 nano-fiber mask, 3D printing allows production and good quality within your reach.
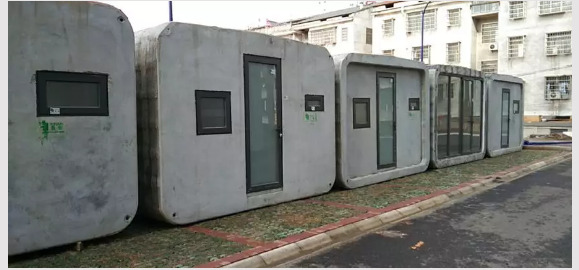
The companies worked together with doctors, engineers, designers to work out the best designs suitable for different types of equipment. The main objective was to develop such products that would match all the required criteria and guidelines set by ‘WHO’.
Tapping The Hidden Potential of 3D Printing
The digitalization especially the cloud facility helped the De-Centralized network to become more robust. Not only local volunteers with 3D printers but engineers and workers all over the world offered their help. The key goal was to make an ergonomic design with the help of various software.
So a company called Carbon™ picked the challenge. They made designs, improved them, tested them, and began to mass-produce them all in 20 day time. Their breakthrough technology DLS™ uses high-quality resin combined with a texture like finish that can outperform any existing products developed via the powder bed technique.
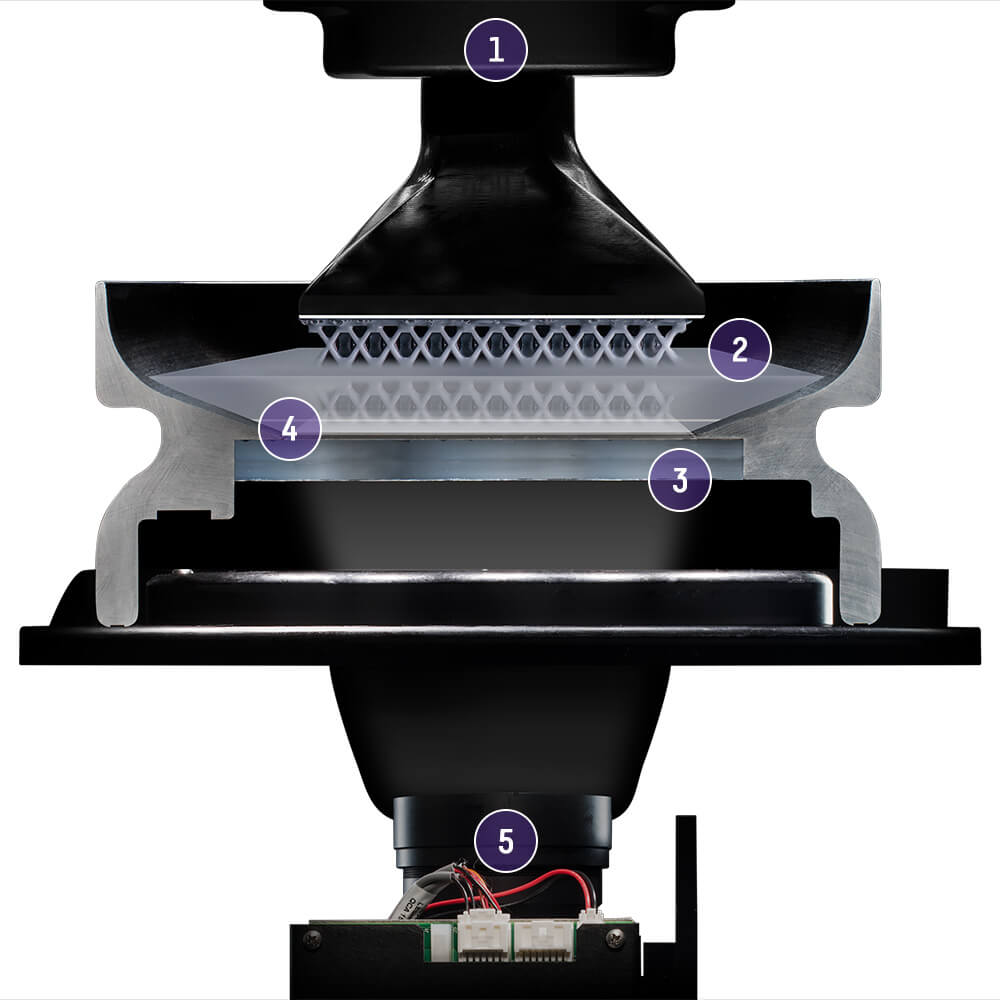
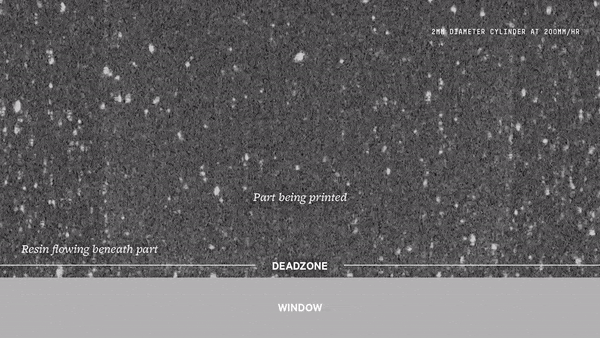
The DLS™ employs light projection, oxygen-permeable optics, to produce exceptional parts. The method called CLIP™ here uses a UV light machine to project cross-sectional parts of the model encoded in UV light at the liquid resin. The resin solidifies when exposed to UV light and oxygen permeates through the filter. The resin on the sides rushes to take the place of solid resin creating a continuous flow of liquid. (Know More about CLIP)
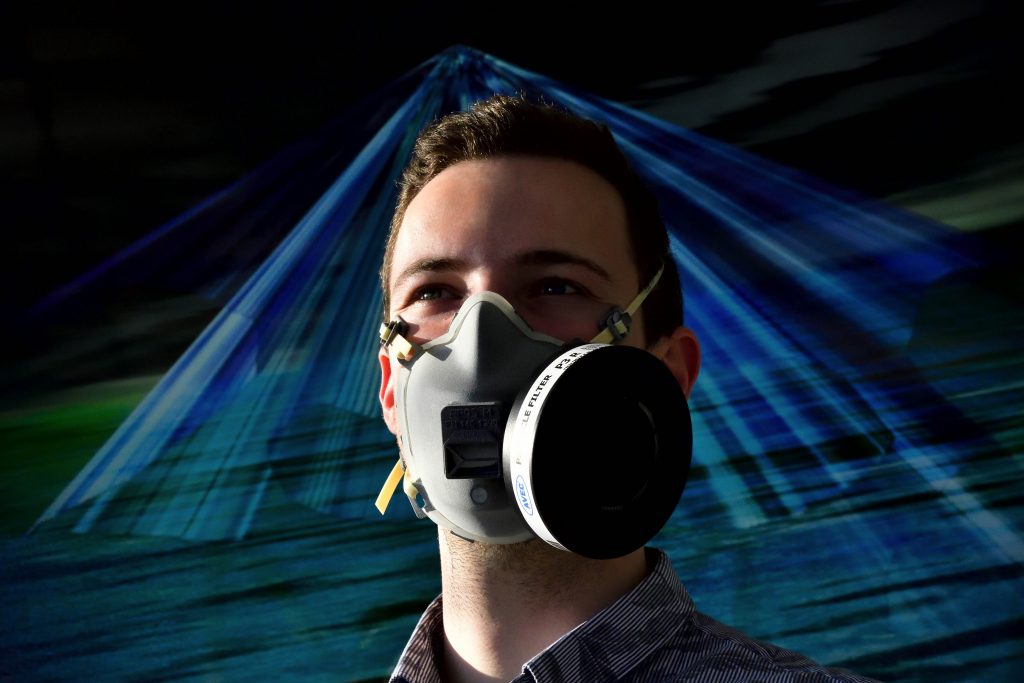
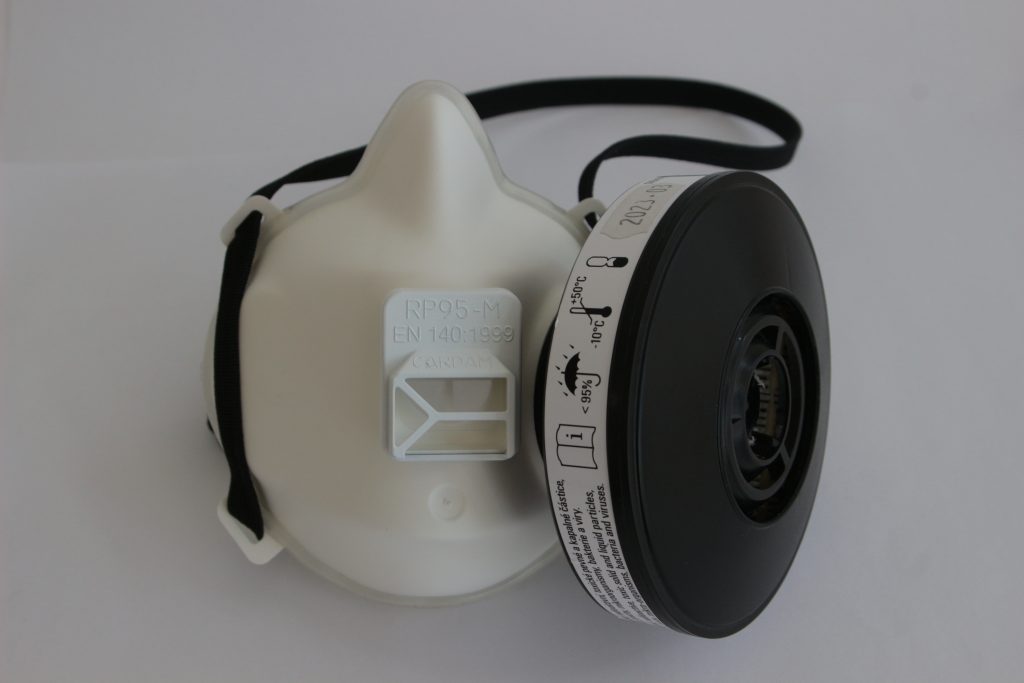
The 3D printing sector also helped hospitals by printing and assembling whole Isolation wards for patients. Many innovations were also made in the area of resin, mask filters, and other products. Recently CTU made a new mask called “RP95-M” which offers the highest degree of protection in the FPP3 level.
Embracing The Challenges
The critical point for this industry was to make the consumers believe that the products they were using were tested and performed equally, or in some cases better than the traditional ones. Another challenge they faced was to ensure that the STEP/STL files were not tampered with. Copyright Infringement was a serious issue they faced since they had to share or upload files to reach more people.
The Core idea of the setup was to help the most affected areas. The FDA also issued an “International Risk Classification system” that provided regulations and ensured the performance and safety of devices. The new designs are approved after keratin tests and new materials are certified for the benefit of 3D printing.
Future 4.0
In the wake of the Covid-19 Pandemic, ADI played a major role in solving the crisis and sprang to action when the world was in a state of emergency. The inherent flexibility and possibility of the 3D printing industry also provide a base for a cleaner and greener future. Advances in developing new materials can make them bio-degradable and tackle the issue of disposal of medical waste in one shot.
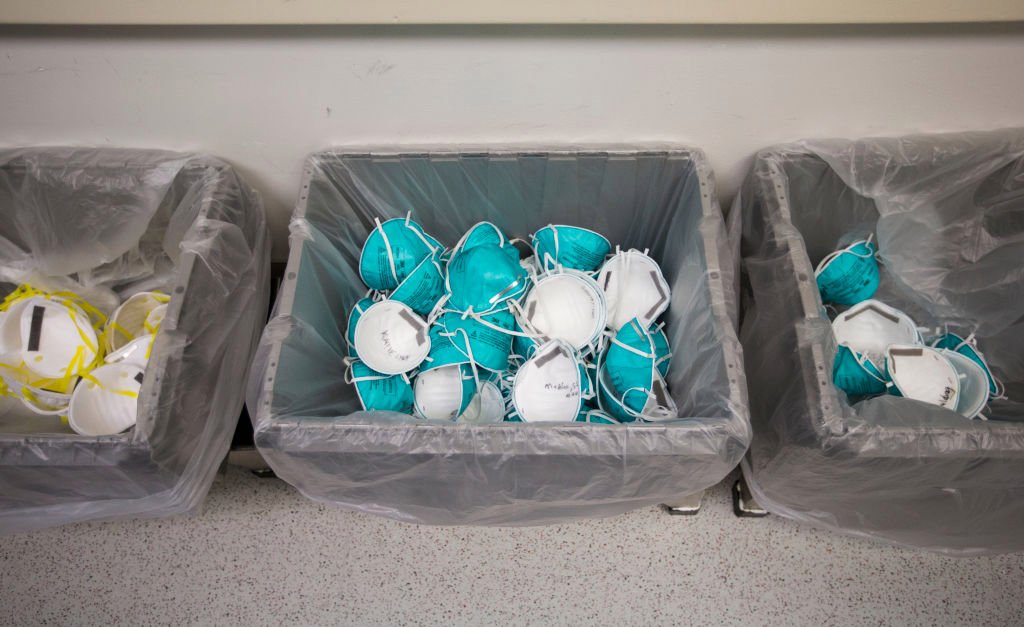
Thanks to its supply-on-demand ability, and digitalization feature it comes very handy whenever needed. Post Pandemic supply chains are expected to be more fragmented, changing the scenario of manufacturing with more investment in the ADI sector. There is no doubt that this industry will be a gold coin for others in the post-pandemic, cyber-physical age.
The Secret of Change is to focus all of your energy, not on fighting the old, but building on the new!
Socrates, Philosopher
I visited many web pages however the audio feature
for audio songs present at this web site is actually marvelous.
Asking questions are genuinely nice thing if you
are not understanding anything fully, however this piece of
writing gives nice understanding even.
whoah this weblog is wonderful i really like reading your articles.
Keep up the good work! You recognize, a lot of people are
searching round for this info, you can aid them greatly.
Here is my blog Madonna